The new article describes in detail certain specific aspects to be taken into consideration by the parties involved in order to ensure the important information is duly communicated in accordance with the relevant regulatory requirements.
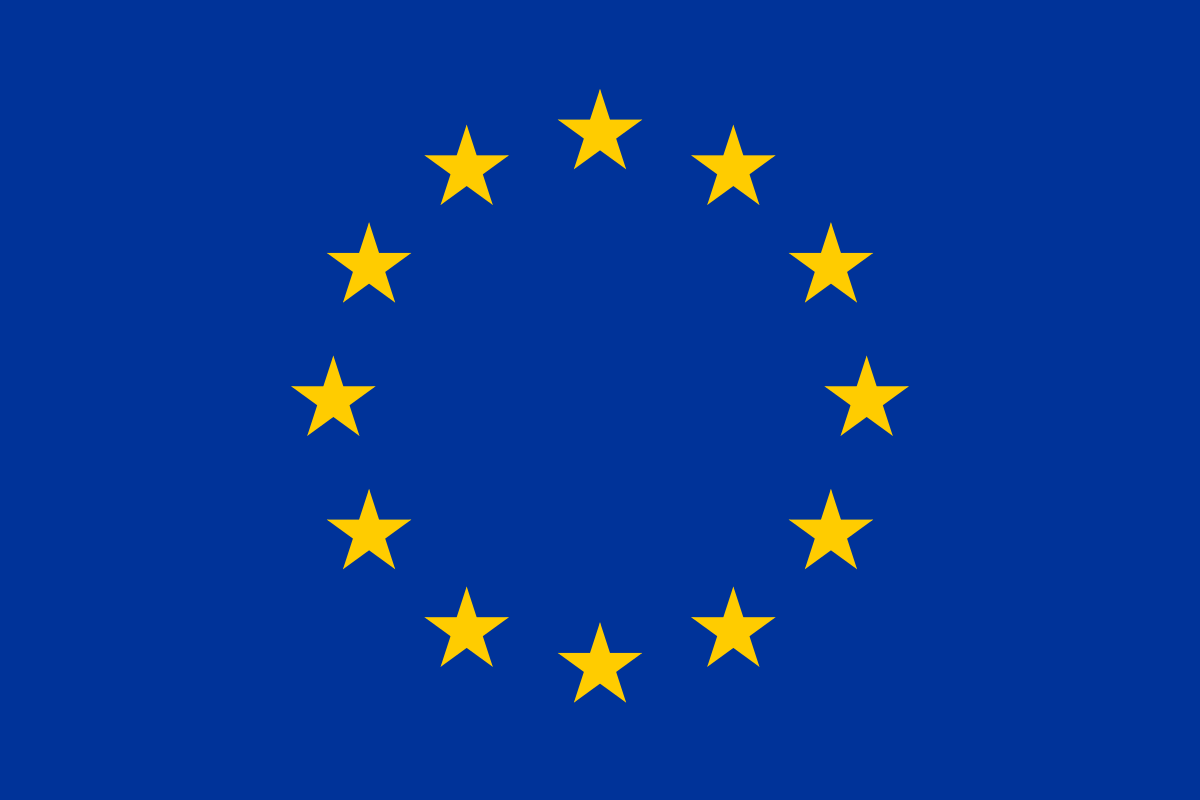
Table of content
The European Commission has issued a guidance document dedicated to the information obligation in case of interruption or discontinuation of supply of certain medical devices and in vitro diagnostic medical devices. Structured as a questions-and-answers document, the guidance provides an overview of the relevant regulatory requirements, as well as additional clarifications and recommendations to be taken into consideration by the parties involved in medical device supply in order to ensure compliance.
At the same time, provisions of the guidance are non-binding in their legal nature, nor they are intended to introduce new rules or impose new obligations. The Commission also reserves the right to make changes to the guidance and recommendations provided therein, should such changes be reasonably necessary to reflect corresponding amendments to the underlying legislation.
Defining Serious Harm from Supply Interruptions or Discontinuations
Under Article 10a (1) of the MDR/IVDR, manufacturers must assess whether an interruption or discontinuation in the supply of their device could lead to “serious harm or risk of serious harm to patients or public health” in one or more Member States. This requirement ensures that essential diagnostic methods or patient therapies are not compromised, as the absence of a specific medical device could directly impact patient care.
Serious harm is defined as any substantial injury to patients or a significant risk to public health, either already occurring or highly probable.
Scenarios in which a device’s unavailability might lead to serious harm include situations where:
- Imminent Risk: Patients could face life-threatening situations without access to the device.
- Serious Deterioration of Health: The device’s absence could lead to significant health deterioration.
- No Available Alternative: Where no suitable alternative therapy or diagnostic method, including pharmaceutical options, is accessible, the lack of the device could severely impact patient outcomes.
Manufacturers should recognize that harm can also arise if healthcare professionals are unable to perform certain medical treatments due to device supply disruptions, further underscoring the need for thorough planning and proactive communication.
Manufacturer’s Approach to Assessing Potential Harm
Manufacturers are responsible for evaluating whether a supply interruption or discontinuation could potentially harm patients or public health. This assessment should be comprehensive and consider the device’s intended population and impact on essential healthcare services.
Key considerations for manufacturers include:
- Population-Based Assessment: Rather than focusing on isolated patient cases, the potential harm should be evaluated at the population level for those relying on the device.
- Information-Based Approach: While a full market analysis isn’t required, manufacturers should use available information on their own device supply to make an informed judgment.
- External Consultation: Manufacturers may consult with healthcare professionals, medical associations, or facilities to obtain further insights into the potential impact on patient safety. This consultation can help gauge the severity and scope of risk if supply is disrupted.
By considering these factors, manufacturers can provide accurate assessments of the consequences of supply disruption and take preventive steps to protect public health.
Indicators for Assessing Serious Harm Potential
To guide manufacturers in evaluating whether an anticipated supply interruption or discontinuation could lead to serious harm, the MDR/IVDR provides several indicators.
While not exhaustive, these indicators can help structure the assessment process:
- Relevance of the Device: Manufacturers should consider the device’s critical role in healthcare. Devices that sustain or save lives, such as life-support systems or accessories, have a higher risk profile if supply is interrupted.
- Intended Patient Population: Devices for vulnerable groups, such as pediatric or geriatric patients, may have more severe consequences if supply is disrupted.
- Treatment Accessibility: If a device interruption limits access to a specific treatment with no alternative options, the manufacturer should consider the heightened risk to patient health.
- Dependency on Device: When patient safety or health outcomes are closely tied to continuous device availability, this dependency raises the risk level associated with any supply disruption.
Alternative Solutions and Successor Devices
When evaluating the risk, manufacturers should also account for available alternatives or successor devices that may mitigate the impact of an interruption:
- Availability of Successors: If a suitable successor device is accessible, manufacturers can consider this option in their assessment. However, the expected duration of the interruption should also be taken into account.
- Training and Infrastructure: Alternative solutions may require specialized infrastructure or training, which could delay their implementation and affect patient care.
- Other Manufacturers’ Alternatives: If the manufacturer is aware of a comparable device from another supplier that can meet demand, this may reduce the risk of harm due to supply disruption.
Other Factors Impacting Supply
Beyond the device’s role and alternatives, additional factors can affect the likelihood and severity of supply interruptions:
- Anticipated Duration: If there’s an objective reason to expect long-term or broad-range interruptions across multiple device models, this may increase risk.
- Market Availability and Stock Levels: Devices already available in the market and existing stock levels should be considered in the risk evaluation.
- Market Share: The manufacturer’s market share of the device also influences the risk; a higher share typically suggests a greater potential impact if supply is disrupted.
- Mitigation Measures: Manufacturers should assess the feasibility of implementing measures to prevent or minimize the effects of supply interruptions, such as increasing production or maintaining stockpiles.
A decision tree diagram can further support the assessment, guiding manufacturers through each critical consideration.
Information Disclosure to Competent Authorities
As explained in the document, information provided to competent authorities under Article 10a of MDR/IVDR is governed by confidentiality rules outlined in Article 109 MDR and Article 102 IVDR. These articles mandate that confidential information is shared judiciously to protect commercial interests while still enabling authorities to maintain public health.
When a competent authority receives a notification, they must share relevant information with other Member States and the European Commission. This collaborative approach ensures that all affected regions are informed and can prepare for potential health system impacts. Authorities may also need to relay information to health institutions, healthcare professionals, importers, and distributors within their jurisdictions.
Providing Information to Competent Authorities
To submit information, manufacturers or their authorized representatives must use the “Manufacturer Information Form,” designed for consistency in notifications across the EU. This form should be submitted to the competent authority in the Member State where the manufacturer or its representative is based.
Member States may also offer additional submission instructions on their respective competent authority websites, ensuring clarity on documentation and procedure requirements. The information submitted should be detailed and specific, as it informs the authority’s response.
Content of the Manufacturer Information Form
Manufacturers are required to include all mandatory information in the Manufacturer Information Form. If circumstances change or additional details become available, manufacturers are encouraged to update the form, labeling new information as “additional” or “follow-up” as indicated in the form’s optional fields.
This flexibility allows for continuous and accurate communication with competent authorities as situations evolve. Optional sections of the form offer space for manufacturers to include any other relevant data that could aid the authority’s assessment.
Detailed and timely updates ensure that authorities remain well-informed and can respond effectively to potential health risks.
Obligations of Other Economic Operators in the Supply Chain
Article 10a (3) of the MDR/IVDR introduces a cascading information requirement throughout the supply chain. Once a manufacturer issues a notification, each economic operator in the chain (importers, distributors, etc.) must pass the information to subsequent operators, health institutions, or healthcare professionals they directly supply. This process must be done “without undue delay”, meaning as quickly as possible without intentional or negligent delays.
Traceability and Responsibility
According to Article 25 of the MDR/IVDR, economic operators are required to maintain traceability records for their devices, identifying both upstream and downstream suppliers. This enables efficient and reliable communication throughout the supply chain, supporting the rapid dissemination of critical information related to supply interruptions.
Application to System and Procedure Packs
For devices included in system or procedure packs, Article 10a applies to the manufacturers of each individual CE-marked component. In cases of a supply interruption, the manufacturer must inform the competent authority and the system or procedure pack producer, who is then responsible for notifying downstream operators, health institutions, and healthcare professionals.
Example of Communication Flow in System and Procedure Packs
Consider a CE-marked device within a surgical pack used only by healthcare professionals. If the manufacturer anticipates a supply interruption, they must notify the relevant competent authority and the party assembling the packs.
This party then informs distributors, who, in turn, pass on the information to health institutions, ensuring a coordinated flow of information.
Conclusion
In summary, the present guidance provides a thorough explanation of the requirements and processes manufacturers must follow to comply with Article 10a, ensuring patient safety through effective communication and risk assessment.
How Can RegDesk Help?
RegDesk is an AI-powered Regulatory Information Management System (RIMS) designed to simplify global compliance for medical device companies. With regulatory intelligence covering 120+ markets, RegDesk helps you prepare and publish global submissions, manage standards, conduct impact assessments, and stay ahead of regulatory changes all from a single, centralized platform. Expanding into new markets has never been easier.