The Food and Drug Administration (FDA or the Agency), the US regulating authority in the sphere of healthcare products, has published a guidance document dedicated to design control. The document covers the regulatory matters related to design verification and validation. In particular, the guidance provides additional clarifications on the applicable regulatory requirements, as well as recommendations to be considered by medical device manufacturers and other parties involved in order to ensure compliance thereto.
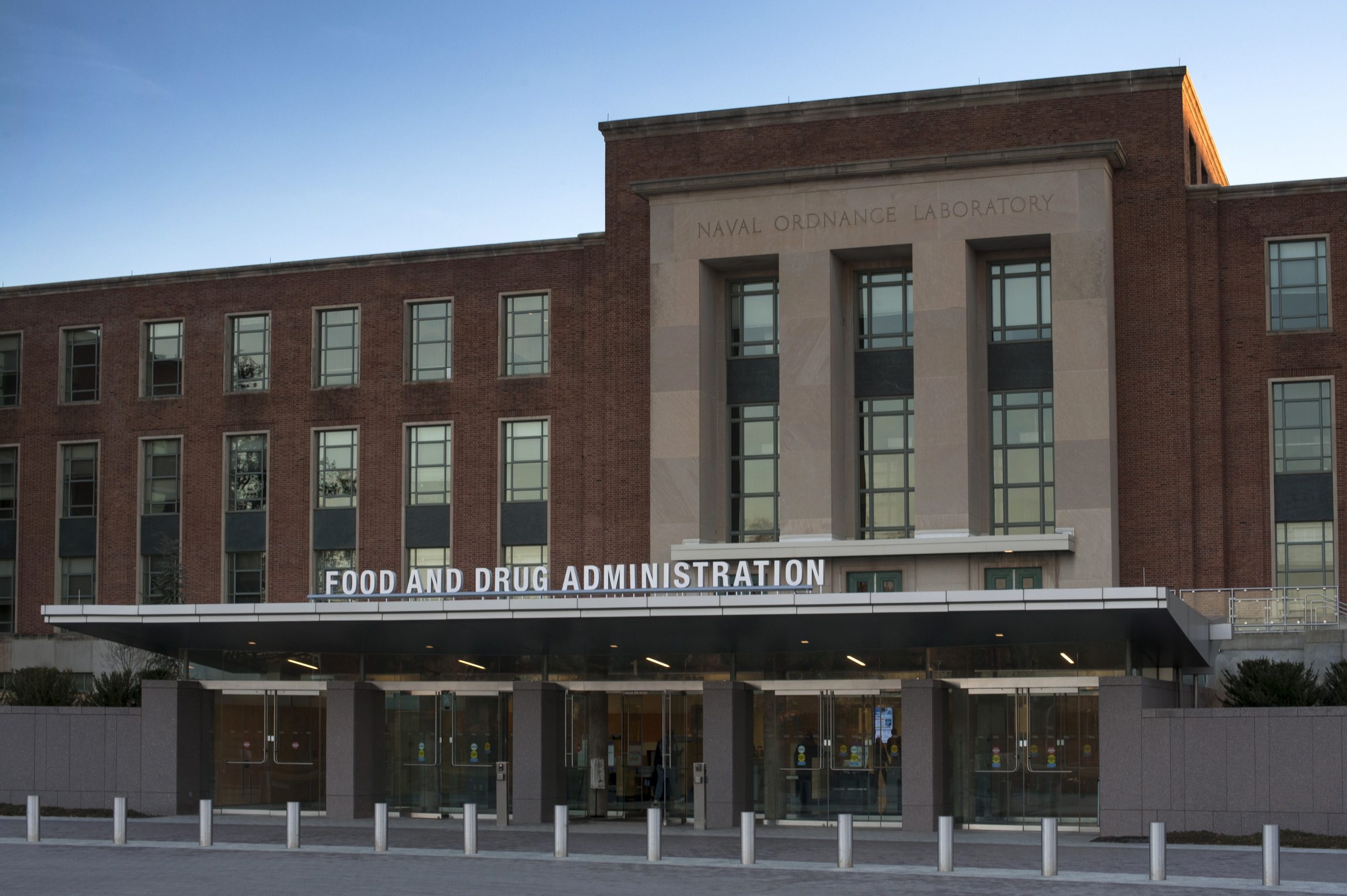
Table of Contents
Regulatory Requirements for Design Validation
According to the applicable legislation, medical device manufacturers are obliged to develop and implement the appropriate procedures for verifying the device design in order to ensure the design output complies with the design input requirements. It is also prescribed that the results of the procedure should be duly documented as a part of the Design History File.
In order to assist medical device manufacturers in interpreting existing regulatory requirements, the document also provides definitions of the most important terms and concepts as set forth by the current legislation, namely:
- Specification means any requirement with which a product, process, service, or other activity must conform.
- Validation means confirmation by examination and provision of objective evidence that the particular requirements for a specific intended use can be consistently fulfilled.
- Process Validation means establishing by objective evidence that a process consistently produces a result or product meeting its predetermined specifications.
- Design Validation means establishing by objective evidence that device specifications conform with user needs and intended use(s).
- Verification means confirmation by examination and provision of objective evidence that specified requirements have been fulfilled.
Key Aspects
The authority states that in spite of close relation to each other, verification and validation have significant differences. Moreover, sometimes medical device manufacturers use different definitions for these terms. The authority encourages their use in the proper context of the quality system requirements.
The document further provides illustrative examples demonstrating the difference between these two concepts, which is the following:
- Verification is intended to confirm that the design output meets the initial design input, which outlines the main design requirements determined at the early development stage. It is stated that each particular solution implemented should be aligned with the general concept of a medical device based on its intended use and applicable safety requirements.
- Validation is intended to conform to compliance on a higher level and is related to the needs of customers. Under this concept, a new medical device should not only meet the generally applicable safety and performance requirements or device-specific design requirements but also address the actual needs of customers or healthcare professionals and solve the issue for which it is intended to be used.
Thus, design verification is closely related to quality assurance as it evaluates the actual implementation of technical solutions. At the same time, validation should take place at later stages and is intended to ensure that each requirement for a particular use is fulfilled.
Types of Verification Activities
According to the document, verification procedures could take place at all the steps of the design development process. It is further stated that the basis of verification is a three-pronged approach involving tests, inspections, and analyses. In the broad understanding, verification covers all the processes intended to ensure the results meet the design input requirements. This goal could be achieved in various ways. The FDA acknowledges that further technological development and advancement resulting in increasing complexity of medical devices requires verification procedures to be improved. It is stated that the particular verification activities to be carried out should depend on the type of design output. The Agency additionally emphasizes that by virtue of this guidance, it does not intend to specify verification activities to be applied but rather to describe the approach to be employed by medical device manufacturers in order to decide on the ones that fit the most according to the particular situation. Some of these activities should be implemented in the development process by default.
In accordance with the guidance, verification methods and activities could include the following:
- Worst-case analysis of an assembly to verify that components are derated property and not subject to overstress during handling and use.
- Thermal analysis of an assembly to assure that international or surface temperatures do not exceed specified limits.
- Fault tree analysis of a processor design.
- Failure modes and effects analysis.
- Biocompatibility testing of materials.
- Bioburden testing of products to be sterilized.
- Comparison of a design to a previous product having an established history of successful use.
As mentioned, the choice of particular methods should be based on the technologies in question. In some cases, it could be subject to strict requirements, while in others, the manufacturer could have certain flexibility in determining the most suitable approach on a case-by-case basis.
The FDA also emphasizes the importance of distinguishing between product testing and verification. In this regard, the authority states that whereas verification testing establishes conformance of design output with design input, the aim of product testing is to determine whether the unit under test has been correctly manufactured. Hence, in spite of certain similarities, these processes are different in their intended purpose. Under the general rule, the testing performed in the context of design verification is far more comprehensive than the one carried out in the course of product testing.
Documentation of Verification Activities
As prescribed by the applicable legislation, the results of design verification activities should be duly documented. In certain cases, documenting the results is required due to the nature of such activities. In this regard, the Agency provides examples of such methods as failure modes or traceability matrix. As it mentioned, verification actives are those carried out by medical device manufacturers in order to ensure the design output complies with the design input. Hence, manufacturers may document the completion of verification activities by linking these activities with the signoff procedures for documents. For instance, it could be prescribed by internal policies implemented by the manufacturer that any and all design output documents should be approved (signed) by the responsible person.
In summary, the present FDA guidance highlights the most important points related to design verification. The authority compares design validation and design verification and provides additional clarifications regarding the current regulatory requirements for the latter in order to assist medical device manufacturers in achieving and sustaining compliance thereto. The document describes the main types of verification activities and outlines their specific features.
Sources:
How Can RegDesk Help?
RegDesk is a next-generation web-based software for medical device and IVD companies. Our cutting-edge platform uses machine learning to provide regulatory intelligence, application preparation, submission, and approvals management globally. Our clients also have access to our network of over 4000 compliance experts worldwide to obtain verification on critical questions. Applications that normally take 6 months to prepare can now be prepared within 6 days using RegDesk Dash(TM). Global expansion has never been this simple.