The Food and Drug Administration (FDA or the Agency), the US regulating authority in the sphere of healthcare products, has published a guidance document dedicated to design control in the context of medical devices. Among other matters, the document addresses aspects related to design verification and validation. Due to their legal nature, guidance documents issued by the FDA are not intended to introduce new rules and requirements the parties involved should follow but provide additional clarifications and recommendations to be considered. In particular, they describe the suggested approach. The parties may apply another approach, provided it complies with any and all relevant regulatory requirements and is approved by the authority in advance. The present article describes in detail the most important regulatory matters related to design validation.
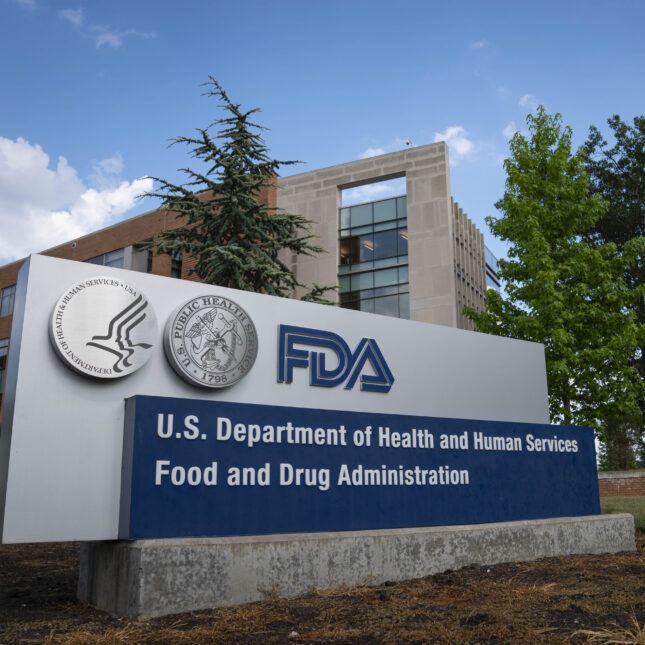
Table of Contents
Regulatory Background
According to the applicable legislation, medical device manufacturers are responsible for developing, implementing, and following procedures for validating the device design. Such activity should be carried out in the context of the appropriate operating procedures employed by a medical devices manufacturer. The FDA also stated that:
- Design validation shall ensure that devices conform to defined user needs and intended uses and shall include testing of production units under actual or simulated use conditions.
- Design validation shall include software validation and risk analysis, where appropriate.
- The results of the design validation, including identification of the design, method(s), the date, and the individual(s) performing the validation, shall be documented in the Design History File.
The guidance also contains references to the appropriate international standards.
In order to assist medical device manufacturers and other parties involved in achieving and sustaining compliance with the regulatory requirements described herein, the guidance provides the definitions of the most important terms and concepts, including the following:
- Specification refers to any requirement with which a product, process, service, or other activity must conform.
- Validation stands for confirmation by examination and provision of objective evidence that the particular requirements for a specific intended use can be consistently fulfilled.
- Process Validation means establishing by objective evidence that a process consistently produces a result or product meeting its predetermined specifications.
- Design Validation means establishing by objective evidence that device specifications conform with user needs and intended use(s).
Design Validation: Key Aspects
The guidance further highlights the most important aspects to be taken into consideration by medical device manufacturers with regard to design validation. As described by the regulating authority, design validation is, in general, intended to ensure the device will meet the particular user needs and will operate as initially intended by its manufacturer. Thus, the aspects related to design validation should be considered starting from the very first steps of the device’s design development process. For this purpose, a medical device manufacturer should identify the key features of the device subject to assessment and then determine the particular validation methods to be applied. In certain cases, it would be reasonable to develop a special schedule providing timing for all the processes and procedures to be performed.
The authority additionally mentions that sometimes in the course of validation, certain deficiencies could be identified in the initial position regarding the user needs. In such a case, the appropriate measures should be taken by a medical device manufacturer in order to address such matters. Depending on the significance of such deficiencies, the decision should be taken – in certain cases, additional corrective actions should be taken.
Validation Methods
The scope of evaluation and testing that medical devices should be subject to depends on the design and complexity of devices and the risks associated thereto. For instance, for some products, clinical trials are not required. At the same time, as stated by the FDA, all devices require clinical evaluation and should be tested in the actual or simulated use environment as a part of validation; this testing should involve devices which are manufactured using the same methods and procedures expected to be used for ongoing production. Apart from testing itself, additional methods of validation could be applied as well, e.g., a compilation of relevant scientific literature or provision of historical evidence.
The Agency also mentions that the scope of device validation should cover the aspects related to packaging and labeling as well, as these elements are also vitally important for ensuring the use of a medical device in a safe and efficient manner. The authority additionally emphasizes that in certain cases, the issues associated with these elements could be identified only after the device has already been placed on the market. Hence, validation to be carried out by the manufacturer should address the matters related to the intended use and storing environment, including the impact of such factors as temperature, humidity, shock and vibration, corrosive atmospheres, etc. This becomes especially important as sometimes the impact the device faces during the transportation is far more significant than the one caused on the device during its use for the initial intended purpose.
As mentioned, the validation should be performed in order to ensure the device meets current user needs. Consequently, it is important to consider the intended users of the device and their qualifications and knowledge. Thus, the approaches to be applied in the case of devices intended to be used by healthcare professionals and laypersons should be different. The authority also emphasizes the importance of distinguishing those who purchase the device from those who will use it. All the points above should be taken into consideration by a medical device manufacturer in the course of design validation.
Validation Documentation
Apart from the aspects described above, the present FDA guidance also pays attention to the matters related to documentation associated with the design validation. In particular, the authority states that validation is a compilation of the results of all validation actives; for a complex design, the detailed results may be contained in a variety of separate documents and summarised in a validation report. The Agency additionally emphasizes the importance of the correct references to other documents the dossier includes.
In summary, the present FDA guidance highlights the key points related to the design validation. The document provides an overview of the applicable regulatory requirements and indicates the particular steps to be taken by medical device manufacturers in order to ensure compliance thereto.
Sources:
How Can RegDesk Help?
RegDesk is a next-generation web-based software for medical device and IVD companies. Our cutting-edge platform uses machine learning to provide regulatory intelligence, application preparation, submission, and approvals management globally. Our clients also have access to our network of over 4000 compliance experts worldwide to obtain verification on critical questions. Applications that normally take 6 months to prepare can now be prepared within 6 days using RegDesk Dash(TM). Global expansion has never been this simple.