The Food and Drug Administration (FDA or the Agency), the US regulating authority in the sphere of medical devices, has published a guidance document dedicated to design control. The document is intended to provide additional clarifications regarding the applicable regulatory requirements, as well as recommendations to be considered by medical device manufacturers and other parties involved in operations with medical devices. Due to its legal nature, the document itself does not introduce new rules or requirements, and the provisions thereof are non-binding. Moreover, the authority states that an alternative approach could be applied, provided such an approach complies with the applicable regulatory requirements and has been agreed with the Agency in advance. The authority also reserves the right to amend the guidance, should it be reasonably necessary to reflect the changes to the application framework.
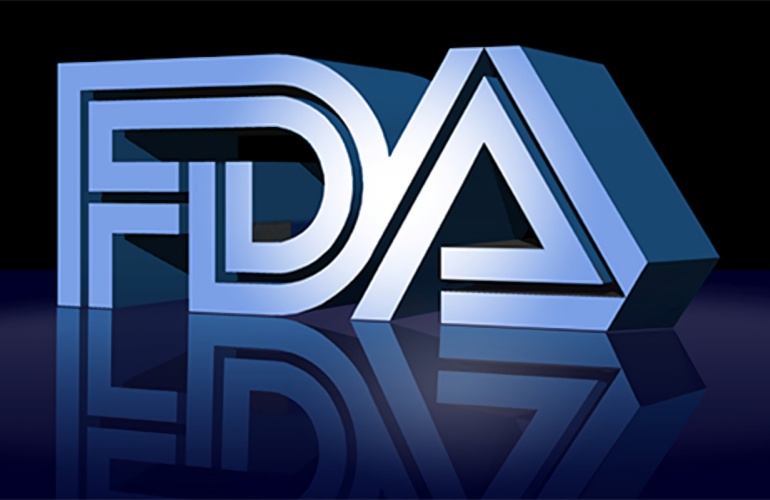
Table of Contents
Design Transfer
According to the existing legislation, each manufacturer shall establish and maintain procedures to ensure that the device design is correctly translated into production specifications. The guidance also provides references to the applicable international standards, namely ISO 9001:1994, and ISO/DIS 13485.
As it is further explained by the Agency, it is vitally important to ensure that any medical devices manufactured are in line with the appropriate product specifications, while any deviations thereof could result in safety- and performance-related issues. Hence, a medical device manufacturer should pay special attention to the way the information about the medical device is being transformed into production specifications. According to the guidance, the level of detail should be determined based on numerous factors, such as the type of medical device to be manufactured, as well as the knowledge and experience of those involved in the process. The guidance provides examples of situations when medical devices are manufactured by third-party contractors who are not involved in the design process, while there could also be situations when devices are produced by the ones who are very familiar with the particular way such devices should be used.
Under the general rule, the scope of “product specifications” covers assembly drawings, component procurement specifications, workmanship standards, manufacturing instructions, and inspection and test specifications. Even if the aforementioned documents are actively used in the process of manufacturing medical devices, there could be other documents describing in detail additional aspects of the manufacturing process, so a manufacturer should be flexible enough in deciding on the approach to be applied to provide information about the medical device and the particular way it should be manufactured. In particular, “product specifications” could be contained in:
- Documentation (in electronic format as well as paper);
- Training materials, e.g., manufacturing processes, test and inspection methods;
- Digital data files, e.g., programmable device files, master EPROM, computer-aided manufacturing (CAM) programming files;
- Manufacturing jigs and aids, e.g., modls, sample wiring harness to be duplicated.
The authority also mentions that the issues associated with the product specifications are usually identified at later stages of the manufacturing process. In particular, once the new design has been just communicated to the production team, its interactions with the design team are efficient enough. However, at later stages, the effectiveness of such cooperation could reduce significantly.
According to the guidance, additional attention should be paid in case a new manufacturing process is to be introduced. The Agency also states that in most cases it is quite difficult to identify potential issues having available only the information regarding the processes related to the prototypes created. The authority explicitly states that the engineering feasibility and production feasibility may be different because the equipment, tools, personnel, operating procedures, supervisions, and motivation could be different when a manufacturer scales up for routine production.
The FDA acknowledges that a design team can’t foresee and prevent all the issues in advance. However, the initial assessment should cover some basic elements including the following ones:
- First, the design and development procedures should include a qualitative assessment of the completeness and adequacy of the product specifications.
- Second, the procedures should ensure that all documents and articles which constitute the production specifications are reviewed and approved.
- Third, the procedures should ensure that only approved specifications are used to manufacture production devices.
The Agency further explains that the very first element is the one to be covered in the course of design transfer, while the others constitute the main principles to be considered. Furthermore, the authority states that in cases when paper documentation is used, a responsible entity should follow standard procedures, while in cases when certain non-traditional means of information are used, additional flexibility will be required.
Design Changes
Apart from design transfer, the present FDA guidance also covers the aspects related to design changes. In this regard, the applicable legislation states that each manufacturer shall establish and maintain procedures for the identification, documentation, valuation or where appropriate verification, review, and approval of design changes before their implementation.
The document further describes that there are two types of control, namely:
- Document control, which describes the way the documents should be drafted and handled.
- Change control, which is related to the approach to be applied about the safety- and performance-related issues, as well as corrective actions taken by the manufacturer in response.
According to the guidance, in a case of a small development project, it would be sufficient to ensure that any corrective actions are duly documented, all the changes introduced do not impact the safety and effectiveness of a product, while all the design documentation is up-to-date. At the same time, in larger projects, the aspects related to cooperation among the parties involved would require more attention.
The principles of document control prescribe that all documents should be duly identified to facilitate navigation and improve their traceability. A list of all the documents should be maintained for the same purpose, while it should be a procedure describing the way the documents are created, maintained, and tracked. Additionally, the manufacturer shall keep records on the history of revisions for the documents. Moreover, it is also necessary to appoint a particular person to be responsible for all the matters related to documents used in the context of design and manufacturing processes.
At the same time, the main principles for change control describe the particular approach to be applied about change requests and change control procedures to be introduced by the manufacturer.
In summary, the present FDA guidance highlights the most important aspects associated with design transfer and justifies the importance of procedures associated thereto. Additionally, the document provides information regrind such concepts as “document control” and “change control”, and also outlines the main distinguishing features. The guidance also clarifies the way the principles of document and change control should be applied for design.
Sources:
How Can RegDesk Help?
RegDesk is a next-generation web-based software for medical device and IVD companies. Our cutting-edge platform uses machine learning to provide regulatory intelligence, application preparation, submission, and approvals management globally. Our clients also have access to our network of over 4000 compliance experts worldwide to obtain verification on critical questions. Applications that normally take 6 months to prepare can now be prepared within 6 days using RegDesk Dash(TM). Global expansion has never been this simple.