The article highlights the key points related to the radiation control legal framework.
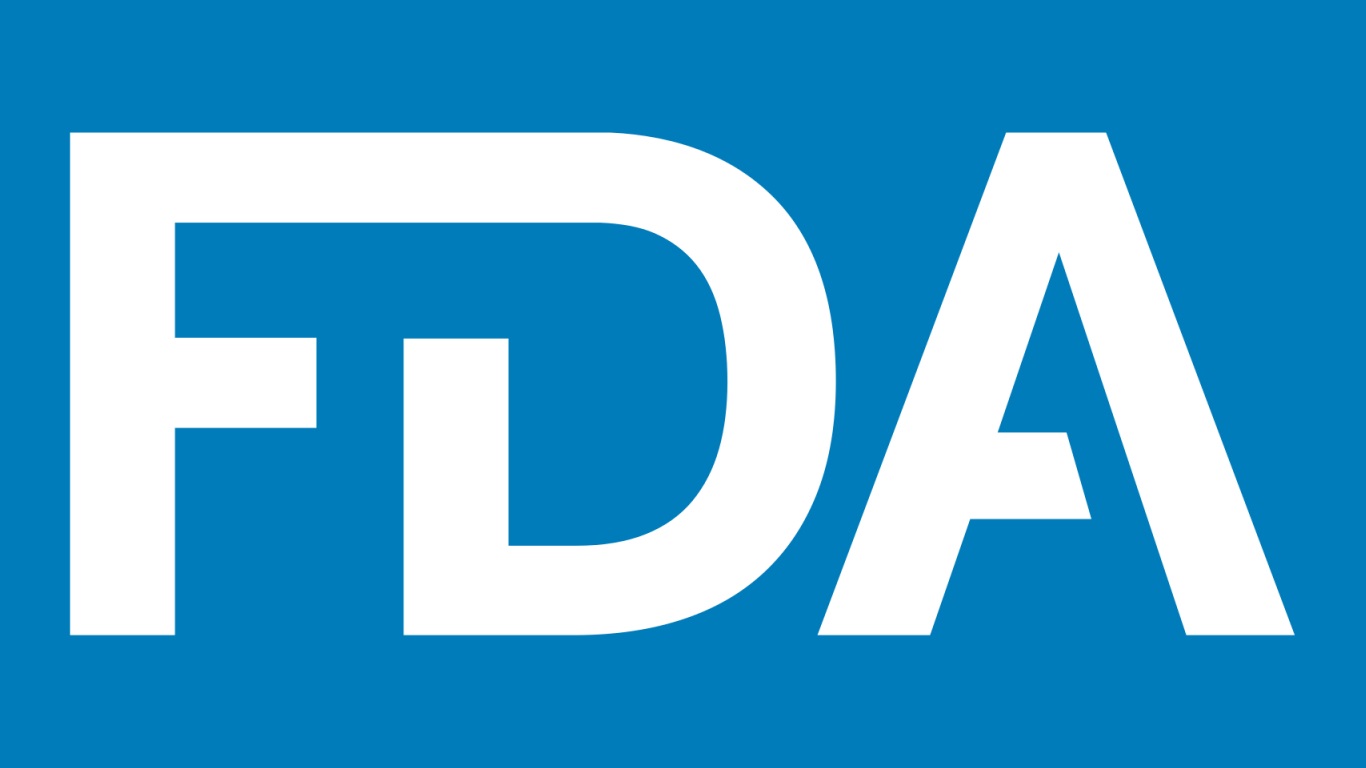
Table of content
The Food and Drug Administration (FDA or the Agency), the US regulating authority in the sphere of healthcare products, has published a guidance document dedicated to radiation control regulations. The document is intended to provide additional clarification and recommendations to be taken into consideration by manufacturers of diagnostic X-ray equipment and other parties involved in order to ensure compliance with the regulatory requirements set forth under the existing legal framework.
At the same time, provisions of the guidance are non-binding in their legal nature, nor are they intended to introduce new rules or impose new obligations. Moreover, the authority explicitly states that an alternative approach could be applied, provided such an approach is in line with the relevant legislation and has been agreed with the authority in advance.
Introduction
The guidance is intended to assist with understanding federal regulations related to diagnostic x-ray equipment. This term encompasses diagnostic x-ray systems and their major components.
It supersedes the 1989 guidance document titled “Clarification of Radiation Control Regulations for Diagnostic X-Ray Equipment” (HHS Publication FDA 89-8221).
Regulatory Background
The FDA, through its Center for Devices and Radiological Health (CDRH), enforces the Electronic Product Radiation Control (EPRC) provisions under the Federal Food, Drug, and Cosmetic Act (FD&C Act). Originally enacted as the Radiation Control for Health and Safety Act of 1968, these provisions were incorporated into the FD&C Act via the Safe Medical Devices Act of 1990.
The regulations outlined in 21 CFR Chapter I, Subchapter J – Radiological Health, govern the manufacturing, importing, installation, recordkeeping, and reporting associated with electronic products. The term “electronic product” is defined in 21 CFR 1000.3(j).
Performance Standards
As it is mentioned by the FDA, the general performance standards for electronic products are outlined in 21 CFR Part 1010, while diagnostic x-ray equipment-specific standards are addressed in:
- 21 CFR 1020.30: Diagnostic x-ray systems and their major components
- 21 CFR 1020.31: Radiographic equipment
- 21 CFR 1020.32: Fluoroscopic equipment
- 21 CFR 1020.33: Computed tomography (CT) equipment
These standards specify the performance requirements for each equipment type, targeting manufacturers, importers, dealers, distributors, and assemblers.
Scope
In accordance with the applicable legislation, diagnostic x-ray systems are dual-classified as both medical devices and electronic products under the FD&C Act. This dual classification subjects them to:
- Medical device provisions, such as sections 510 and 520 of the FD&C Act (21 U.S.C. §§ 360 and 360j).
- EPRC provisions and associated regulations for electronic products.
The present guidance is divided into two main sections:
- General Section (Section IV): Covers broad regulatory and compliance topics related to diagnostic x-ray equipment.
- Specific Section (Section V): Focuses on detailed requirements within the performance standards outlined in 21 CFR 1020.30 through 1020.33.
It is important to mention that the document exclusively addresses requirements under the EPRC provisions and their implementing regulations. It does not encompass requirements related to the regulation of diagnostic x-ray equipment as medical devices.
Manufacturers seeking information on medical device regulations for diagnostic x-ray equipment are advised to consult the FDA website for further details.
Harmonization and Global Compliance
The FDA acknowledges the complexities global manufacturers face in meeting varied regulatory requirements. To streamline compliance, the FDA seeks to align its diagnostic x-ray equipment regulations with International Electrotechnical Commission (IEC) standards where feasible.
This harmonization is intended to facilitate efficient and consistent regulatory review processes.
Related Guidance Documents
Manufacturers are encouraged to review additional FDA guidance documents, such as:
- Medical X-Ray Imaging Devices Conformance with IEC Standards
- Policy Clarification for Certain Fluoroscopic Equipment Requirements
Furthermore, the authority encourages all the parties involved to monitor on a regular basis its websites to be aware of the recommendations published therein from time to time.
Conclusion
In summary, the present FDA guidance serves as a vital resource for industry stakeholders, clarifying regulatory requirements and performance standards for diagnostic x-ray equipment. It underscores the authority’s commitment to simplifying compliance, harmonizing standards and ensuring that manufacturers have the tools and information needed to navigate the regulatory landscape effectively.
How Can RegDesk Help?
RegDesk is an AI-powered Regulatory Information Management System (RIMS) designed to simplify global compliance for medical device companies. With regulatory intelligence covering 120+ markets, RegDesk helps you prepare and publish global submissions, manage standards, conduct impact assessments, and stay ahead of regulatory changes all from a single, centralized platform. Expanding into new markets has never been easier.