The new article describes certain specific aspects related to the regulatory framework for the designation of conformity assessment bodies in terms of regulatory requirements applicants should meet.
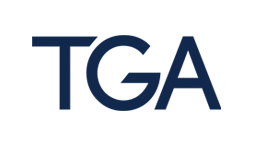
Table of content
The Therapeutic Goods Administration (TGA), an Australian regulating authority in the sphere of healthcare products, has published a guidance document dedicated to determinations for Australian conformity assessment bodies. The document provides a general overview of the applicable regulatory requirements, as well as additional clarifications and recommendations to be taken into consideration by medical device manufacturers and other parties involved in order to ensure compliance.
At the same time, provisions of the guidance are non-binding in their legal nature, nor are they intended to introduce new rules or impose new obligations. The authority also reserves the right to make changes to the guidance and recommendations provided therein, should such changes be reasonably necessary to reflect corresponding amendments to the underlying legislation.
In particular, the document outlines the essential requirements for an Australian company seeking to become an Australian Conformity Assessment Body (CAB) and the standards to be maintained once the determination has been issued. These requirements are set out in Schedule 3AA of the Medical Device (MD) Regulations.
Key Requirements
The document describes in detail specific requirements an interested organization should meet in order to be eligible for designation.
According to the guidance, the applicant entity should:
- Employ personnel with the necessary technical, scientific, and clinical competence.
- Maintain facilities and processes that enable the assessment and issuance of conformity assessment certificates within the scope of the determination.
- Undertake post-certification activities, including monitoring and surveillance of certified manufacturers throughout the audit cycle.
- Ensure independence and impartiality in all operations.
- Avoid actual or perceived conflicts of interest in relation to manufacturers for whom certification-related activities are performed.
- Maintain adequate general liability insurance.
- Implement and maintain an effective quality management system (QMS).
- Document and disclose the nature and management of any relationships between other legal entities within the same larger organization that may impact actual or perceived independence and impartiality.
Alignment with International Standards
The document also pays special attention to the efforts taken to harmonize the local regulatory requirements with the ones implemented in other countries. As explained by the TGA, the Australian CAB framework aims to align with European Union (EU) requirements for notified bodies as defined in Annex VII of the European Medical Devices Regulation 2017/745 (EU MDR) and the In Vitro Diagnostic Regulation 2017/746 (EU IVDR).
These regulations came into force on May 25, 2017. The requirements also align with the Medical Device Single Audit Program’s (MDSAP) criteria for auditing organizations (AO) and implement recommendations from the International Medical Device Regulators Forum (IMDRF) Good Regulatory Review Practices (GRRP) working group.
Detailed Requirements
In order to assist the parties involved, the guidance further provides a detailed breakdown of requirements to be taken into consideration when applying for designation. Organizational and General Requirements cover such aspects as:
- Structure of the Australian CAB, including assignment of responsibilities, independence, impartiality, confidentiality, financial resources, and liability.
- Quality management system (QMS) requirements.
- Resource requirements relating to the competence, availability, authorization, monitoring, and training of personnel and external resources undertaking certification-related activities, outsourcing arrangements, and related facilities and equipment.
Process Requirements are applicable to:
- Documented processes and procedures for conducting certification-related activities.
Modifications and Specific References are intended to address:
- Terminology differences between Australia and Europe.
- Incorporation of references to Australian regulatory requirements for manufacturers.
- Removal of requirements not relevant to Australian CABs.
Best Practice Documents
The guidance also contains references to other “best practice” documents that establish expectations and details for interpreting requirements, implementing processes, and producing regulatory outputs.
These may include:
- International standards (e.g., ISO17021-1)
- Guidance documents published by the EU Medical Devices Coordination Group (MDCG)
- IMDRF guidelines
- MDSAP consortium documents
- Legacy documents from the Global Harmonisation Task Force (GHTF)
Scope of Determination
An Australian CAB determination may allow certification of the full range of Australian conformity assessment procedures and all types of medical devices (including IVDs), or a limited range of procedures for specified types of medical devices. The authority additionally emphasizes that the scope will only include procedures and device types for which adequate resources and competence have been demonstrated.
Conformity Assessment Procedures
According to the guidance, the scope of conformity assessment procedures a CAB may undertake would also depend on the products it will deal with.
For general medical devices the relevant conformity assessment procedures for medical devices, as set out in Schedule 3 of the MD Regulations, include:
- Part 1: Full quality assurance procedures, including clause 1.6 (examination of design)
- Part 1: Full quality assurance procedures, excluding clause 1.6 (examination of design)
- Part 2: Type examination procedures
- Part 3: Verification procedures
- Part 4: Production quality assurance procedures
- Part 5: Product quality assurance procedures
For in vitro diagnostics (IVDs), the relevant conformity assessment procedures for IVDs include:
- Part 1: Full quality assurance procedures, including clause 1.6 (examination of design)
- Part 1: Full quality assurance procedures, excluding clause 1.6 (examination of design)
- Part 2: Type examination procedures
- Part 4: Production quality assurance procedures
Device Types and Codes
As it is stated in the document, the scope of medical devices included in a determination will be specified using the list of codes and corresponding types of devices/technologies defined in the EU’s Commission Implementing Regulation (EU) 2017/2185:
- Annex I of EU Regulation 2017/2185 defines the codes and corresponding device types for non-IVD medical devices
- Annex II defines the codes and corresponding device types for IVDs
Conclusion
In summary, the present guidance document issued by the TGA provides a detailed clarification on certain regulatory matters related to the designation of conformity assessment bodies in line with the existing legal framework. The document specifies the requirements interested parties should meet in order to be eligible for designation and also to comply with the relevant requirements they will be subject to upon designation.
How Can RegDesk Help?
RegDesk is an AI-powered Regulatory Information Management System that provides medical device companies with regulatory intelligence for over 120 markets worldwide. It can help you prepare and publish global applications, manage standards, run change assessments, and obtain real-time alerts on regulatory changes through a centralized platform. Global expansion has never been this simple.