The article highlights the key points related to the application of certain essential principles intended to ensure the safety and proper performance of healthcare products allowed to be marketed and used in Australia.
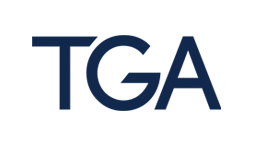
Table of content
The Therapeutic Goods Administration (TGA), an Australian regulating authority in the sphere of healthcare products, has published a guidance document dedicated to the Essential Principle 13B. The document provides an overview of the applicable regulatory requirements, as well as additional clarifications and recommendations to be taken into consideration by medical device manufacturers and other parties involved in order to ensure compliance.
At the same time, the authority reserves the right to make changes to the guidance and recommendations provided, should such changes be reasonably necessary to reflect corresponding amendments to the underlying legislation.
In particular, the guidance document dated 26 July 2024, addresses the interpretation and application of Essential Principle (EP) 13B for medical device software in Australia. This guidance is crucial for sponsors, manufacturers, and software developers to ensure their medical devices meet the necessary regulatory requirements for safety, quality, and performance under Australian law.
Essential Principles Overview
Under the general rule, in order to legally supply a medical device in Australia, manufacturers and sponsors must demonstrate that their device complies with the Essential Principles (EPs) as stipulated in the Therapeutic Goods Act 1989 and the Therapeutic Goods (Medical Devices) Regulations 2002. These principles are mandatory legislative requirements that outline the safety and performance characteristics essential for medical devices.
The Essential Principles are divided into general and specific categories. There are six general EPs that apply universally to all medical devices, while nine additional EPs focus on the design and construction of medical devices on a case-by-case basis. For detailed information, stakeholders are advised to refer to the Essential Principles checklist.
Changes from February 2021
The regulations incurred significant amendments in December 2019, specifically addressing software-related requirements. These changes took effect on 25 February 2021 and included updates to the EPs, most notably the introduction of EP 13B.
This new principle mandates that the current version and build number of any medical device software, or device incorporating software, must be accessible and identifiable to users. The required information must be presented in English and can also be provided in additional languages if necessary.
To accommodate devices already included in the Australian Register of Therapeutic Goods (ARTG), transition arrangements were implemented, requiring full compliance with EP 13B by November 2024. It is important to note that no transitional provisions exist for EPs 12.1 and 13.2(3) since these amendments were clarifications of existing requirements rather than new obligations.
Software Version Numbers and Build Numbers
EP 13B specifically addresses the traceability of medical device software through the implementation of version and build numbers. These identifiers must be accessible and easily identifiable by users, ensuring that all software-based medical devices, including firmware and Software as a Medical Device (SaMD), comply regardless of their complexity or functions.
As explained by the TGA, version and build numbers serve as vital tools for identifying and tracing software throughout its lifecycle. These identifiers are essential for manufacturers, developers, sponsors, healthcare professionals, and regulatory bodies to monitor and manage the software from conception through to end-of-life.
Traceability is crucial for detecting device-specific adverse events and taking efficient post-market actions. Furthermore, traceability helps demonstrate compliance with other applicable EPs, including EP 12.1, which pertains to the implementation of appropriate design controls and processes for ongoing product improvements throughout the software lifecycle.
The Therapeutic Goods (Medical Devices) Regulations 2002 do not require the use of a specific version and build numbering convention, allowing manufacturers flexibility in how they demonstrate compliance with EP 13B. Figure 1 in the original guidance document provides an example of a common convention known as semantic versioning, which follows the format: major.minor.version.build.
For medical devices that operate across multiple platforms, manufacturers may include relevant information about the operating system within the version and build number to ensure clarity for users. For instance, as illustrated in Figure 2, the version 92.0.902.7201 of Beans AutoScan DX is associated with the BeanOS 32-bit operating system, distinguishing it from a potential version developed for a 64-bit system.
Documenting the Version and Build Number Convention
Manufacturers are encouraged to document and explain the version and build number convention they choose to use. This explanation, along with instructions on where users can find the version and build number, should be included in the information accompanying the medical device.
Conclusion
In summary, the present guidance is essential for all stakeholders involved in the development, manufacturing, and distribution of software-based medical devices in Australia. Compliance with the requirements of EP 13B ensures that these devices meet the highest standards of safety, quality, and performance.
How Can RegDesk Help?
RegDesk is an AI-powered Regulatory Information Management System (RIMS) designed to simplify global compliance for medical device companies. With regulatory intelligence covering 120+ markets, RegDesk helps you prepare and publish global submissions, manage standards, conduct impact assessments, and stay ahead of regulatory changes all from a single, centralized platform. Expanding into new markets has never been easier.