The article highlights the key points related to the regulatory requirements for in vitro diagnostic (IVD) medical devices manufactured by healthcare institutions to address their internal needs.
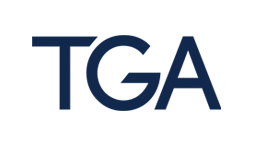
Table of content
The Therapeutic Goods Administration (TGA), an Australian regulating authority in the sphere of healthcare products, has published a guidance document dedicated to the regulatory status for in-house IVDs. The present document provides an overview of the requirements set forth under the existing legal framework, as well as additional clarifications and recommendations to be taken into consideration by the parties involved.
At the same time, the authority reserves the right to make changes to the guidance and recommendations provided therein, should such changes be reasonably necessary to reflect corresponding amendments to the underlying legislation.
Regulatory Background
First of all, the authority emphasizes the importance of ensuring that Australian laboratories manufacturing in-house in vitro diagnostic medical devices (IVDs) adhere to regulatory requirements established on July 1, 2010. These requirements ensure the legal supply of in-house IVDs within Australia.
The regulatory framework incorporates essential principles for the quality, safety, and performance of IVDs, a risk-based classification scheme, conformity assessment procedures, compliance with recognized standards, and provisions for post-market activities, including monitoring and adverse event reporting. The TGA collaborates with the National Association of Testing Authorities (NATA) under a Memorandum of Understanding (MoU) to regulate in-house IVDs.
Definition and Scope of In-house IVDs
According to the guidance in-house IVDs are pathology tests developed or modified within a laboratory or laboratory network for testing human samples, intended to assist in clinical diagnosis or management decisions.
These IVDs, if supplied outside the originating laboratory or network, are classified as commercially supplied IVDs and must be included in the Australian Register of Therapeutic Goods (ARTG) before external supply. The regulations extend beyond medical testing laboratories to all laboratories manufacturing in-house IVDs in Australia.
Any tests for therapeutic purposes, including diagnostic, screening, susceptibility, or disease monitoring tests, are subject to the in-house IVD regulatory framework, regardless of Medicare rebate status. In-house tests developed solely for research purposes, without patient/client result reporting, are not considered IVDs.
Categories of In-house IVD Development
The document further outlines special categories of in-house IVDs as set forth under the applicable legislation, namely:
Developed from First Principles (De Novo)
An in-house IVD developed from first principles involves the laboratory or network being responsible for its design and production, including:
- Design control with the assignment of specifications.
- Assembly, processing, and packaging of components.
- Assigning the intended purpose through accompanying information (instructions for use or laboratory-controlled documents).
Developed or Modified from Published Sources
This category includes IVDs produced by a laboratory or network based on:
- Scientific literature.
- Design specifications from another laboratory’s in-house IVD.
- Any other source’s design specifications.
Such IVDs may involve assembling commercially supplied components that are not finished products, not presented as IVDs, or marked for research/investigational use only.
The laboratory is responsible for:
- Assembly, processing, and packaging of separate components.
- Assigning the intended purpose through supplied information.
- Supplying the in-house IVD under the laboratory’s name.
Modifications to Commercially Supplied IVDs
Commercially supplied IVDs become in-house IVDs when:
- Used for a clinical purpose other than the manufacturer’s intent.
- Modified physically in any way.
- Used contrary to the manufacturer’s instructions.
The authority additionally emphasizes that laboratories must document and validate any changes to ensure the assay’s safety and effectiveness. Validation requirements for class 1 – 3 in-house IVDs are specified by the National Pathology Accreditation Advisory Council (NPAAC).
If a laboratory imports and modifies a commercial IVD, it becomes the sponsor and must apply for its inclusion in the ARTG.
Modifications that Create In-house IVDs:
- Dilution of reagents beyond manufacturer specifications.
- Substitution of kit components with alternatives.
- Use of alternative control materials not specified by the manufacturer.
- Modification of cut-off values or calculation methods.
- Use of different specimen types than those specified.
Modifications that Do Not Create In-house IVDs:
- Variations included by the manufacturer.
- Use of alternative controls specified by the manufacturer.
- Establishment of alternative reference ranges through documented processes.
These latter modifications do not result in regulatory in-house IVDs but must still be verified per the laboratory’s quality management system and accreditation requirements.
Compliance and Responsibilities
As further explained by the authority, laboratories manufacturing in-house IVDs must ensure:
- Compliance with the essential principles for quality, safety, and performance.
- Adherence to risk-based classification schemes.
- Application of appropriate conformity assessment procedures.
- Utilization of recognized standards to demonstrate compliance.
- Implementation of post-market surveillance, including adverse event reporting.
The TGA, in collaboration with NATA, oversees the enforcement of these regulatory requirements, ensuring laboratories meet all stipulated criteria, while the appropriate guidance provided assists laboratories in understanding and fulfilling their obligations under the in-house IVD regulatory framework.
Conclusion
In summary, the present TGA guidance is designed to provide additional clarifications regarding the rules and requirements laboratories should follow with respect to the in vitro diagnostic medical devices they are using in their day-to-day activity.
How Can RegDesk Help?
RegDesk is an AI-powered Regulatory Information Management System that provides medical device companies with regulatory intelligence for over 120 markets worldwide. It can help you prepare and publish global applications, manage standards, run change assessments, and obtain real-time alerts on regulatory changes through a centralized platform. Global expansion has never been this simple.